
FORENSIC
ENGINEERING INVESTIGATIONS
Our forensic engineering investigations provide a thorough and evidence-based analysis of system failures, operational issues, and compliance concerns. With expertise in mechanical, electrical, plumbing, and fire protection systems, we help clients identify root causes, make informed repair decisions, and implement preventive solutions to avoid future issues, enhancing system reliability and safety across diverse applications.

Our approach to forensic engineering addresses both immediate issues and long-term performance, ensuring efficient, safe, and code-compliant systems. Clients benefit from clear diagnostics and actionable insights, enabling confident decisions about repairs, retrofits, or system enhancements.
Targeted Analysis for Lasting Reliability
Our forensic MEP/FP investigations cover a range of specialized services, addressing specific system challenges such as identifying electrical failures, assessing HVAC performance, and troubleshooting plumbing leaks. Each feature below plays a key role in providing reliable, actionable findings that help clients optimize performance and address system vulnerabilities effectively.
HVAC System Performance Assessment
Diagnoses inefficiencies and failures in heating, ventilation, and air-conditioning systems.
Fire Protection System Evaluation
Reviews fire protection systems to ensure reliability and compliance.
Water Quality and Backflow Prevention Analysis
Ensures plumbing systems maintain water quality and prevent backflow contamination.
Electrical System Analysis
Assesses electrical systems for failures, safety risks, and compliance with regulations.
Root Cause Failure Analysis for MEP Systems
Investigates the underlying causes of system failures to guide effective corrective actions.
Vibration and Acoustic Analysis for Mechanical Systems
Examines the impact of vibrations and noise on mechanical system performance and occupant comfort.
Plumbing Leak and Corrosion Analysis
Detects sources of leaks and corrosion, preventing water damage and system failures.
Environmental and Mechanical Impact Assessment
Examines environmental factors affecting MEP systems’ performance and durability.
Documentation and Reporting
Provides comprehensive reports for insurance, litigation, and compliance.
HVAC System Performance Assessment
-
Root Cause of Performance Issues: Diagnoses problems like inadequate cooling, heating, or airflow by analyzing equipment and control settings. For instance, if a commercial building experiences uneven cooling across floors, this analysis can reveal the cause, such as duct obstructions, thermostat calibration errors, or outdated components, and recommend targeted fixes to restore optimal comfort.
-
Component Failure and Wear Analysis: Assesses individual HVAC components (e.g., compressors, fans, dampers) for early signs of wear or failure. This is essential in situations where equipment frequently breaks down, causing costly downtime. By identifying faulty components in advance, building owners can proactively replace or repair them, preventing unexpected shutdowns and ensuring a more reliable system.
-
Energy Efficiency Optimization: Evaluates how well the HVAC system uses energy and recommends adjustments to improve efficiency. In buildings with high energy bills, this assessment helps reduce costs by identifying areas where efficiency can be improved, such as by recalibrating controls or upgrading to energy-efficient components, ultimately saving energy and extending equipment life.
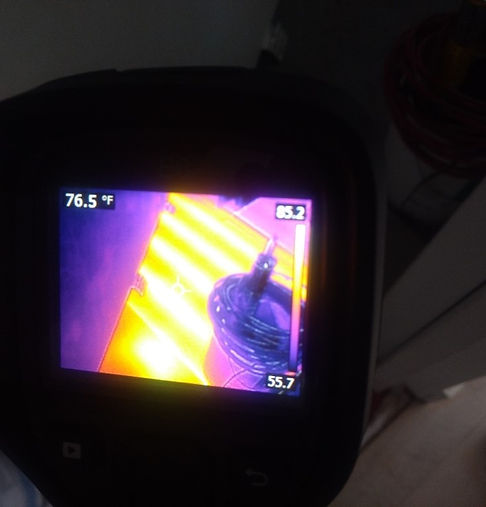_.jpg)
Electrical System Analysis
-
Fault Detection and Load Evaluation: Identifies issues like short circuits, overloads, or grounding problems that could lead to safety hazards or power outages. In facilities with high electrical demands, like hospitals or data centers, this evaluation ensures that systems can operate safely without the risk of unexpected blackouts, protecting both sensitive equipment and occupant safety.
-
Capacity and Load Verification: Verifies that the electrical system can handle current and future loads without risking overloading. This is particularly important in facilities planning equipment upgrades or expansions, where verifying load capacity ensures that the system can support additional demands without the need for a costly system overhaul.
-
Compliance and Safety Assurance: Confirms that the electrical system meets applicable codes and safety standards, reducing legal and operational risks. For instance, in older buildings, an inspection may uncover wiring that no longer meets current codes, allowing property owners to address these issues proactively to avoid fines and ensure occupant safety.
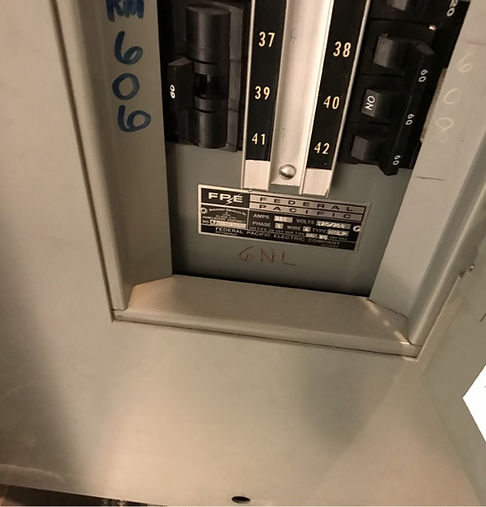.jpg)
Plumbing Leak and Corrosion Analysis
-
Leak Source Identification: Uses advanced detection methods to pinpoint leaks within walls, floors, or underground pipes. This is essential in cases where unexplained water damage appears, such as wet patches on walls or ceilings, helping facility managers address hidden leaks quickly before they cause significant structural or mold damage.
-
Corrosion Detection and Preventive Health Planning: Examines pipes and fixtures for early signs of corrosion or material degradation, providing tailored solutions to prevent future issues. In settings like commercial kitchens, where exposure to grease and chemicals can speed up corrosion, this analysis recommends durable materials and maintenance routines to keep systems functioning optimally and reduce repair costs over time.
-
Backwater Valve Failure Prevention: Evaluates backwater valves to prevent sewer backup issues, analyzing common failure causes like blockages, wear, or improper installation. This feature is crucial in flood-prone areas or buildings with below-grade plumbing, ensuring wastewater doesn’t flow back into the property, safeguarding interiors and maintaining sanitation standards.

Fire Protection System Evaluation
-
System Functionality and Readiness Testing: Tests critical components like sprinklers, alarms, and valves to confirm that they activate correctly during an emergency. For instance, in a high-occupancy building, this testing is vital to ensure reliable performance during a fire, safeguarding lives and property.
-
Code and Standards Compliance Verification: Checks that systems align with NFPA and local fire codes, which is essential for both safety and legal compliance. In newly renovated or repurposed buildings, this assessment helps ensure that fire protection systems meet updated codes, avoiding penalties and reducing liability.
-
Preventive Maintenance Recommendations: Provides customized maintenance plans to keep systems in optimal condition. For example, in large warehouses where fire protection may not be frequently inspected, these recommendations ensure that equipment remains functional, reducing the risk of malfunction during a fire.
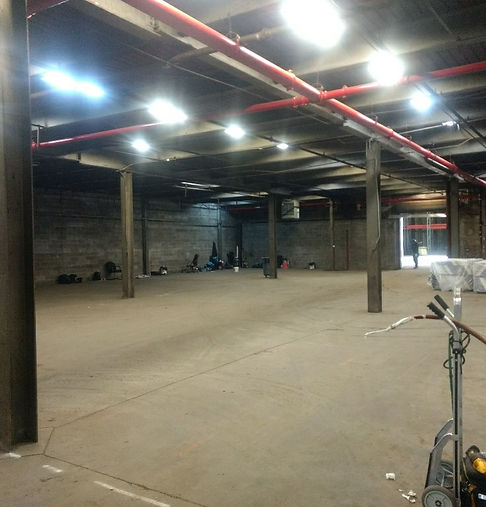
Root Cause Failure Analysis
-
Thorough Incident Analysis: Examines the series of events leading to system failures, pinpointing specific causes and underlying issues. For instance, if an HVAC system frequently malfunctions during high-demand periods, this analysis might uncover inadequate system capacity or control issues, allowing facility managers to address these problems before further damage occurs.
-
Customized Solutions for System Improvement: Provides targeted recommendations tailored to the specific issues identified. In a manufacturing plant, for example, where a piece of equipment continually breaks down, this analysis might suggest adjusting settings or replacing specific components to improve performance.
-
Cost-Effective Repair Guidance: Prioritizes necessary repairs or upgrades to avoid unnecessary expenses. For example, in office buildings with frequent HVAC breakdowns, this guidance helps owners address core issues without a full system replacement, optimizing repair budgets.
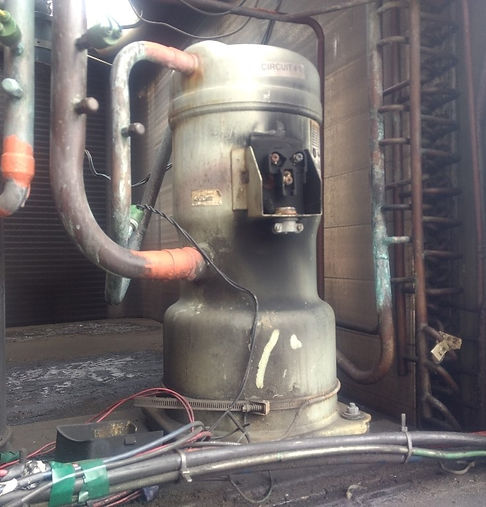_.jpg)
Environmental and Mechanical Impact Assessment
-
Impact of Climate and Temperature: Assesses how extreme weather or temperature fluctuations impact system performance, especially valuable for facilities in harsh climates. For instance, in areas with freezing temperatures, this analysis may recommend additional insulation or protective enclosures for vulnerable pipes and equipment.
-
Vibration and Structural Stress Analysis: Studies vibrations from equipment or surrounding infrastructure that may lead to wear or connection issues. This is crucial in high-rise buildings, where structural sway can impact MEP systems, helping to avoid premature wear or noise disturbances by implementing dampening solutions.
-
Recommendations for Durability: Suggests enhancements to make systems more resilient to environmental conditions. In locations with high humidity, this might include advising corrosion-resistant materials or dehumidification strategies, reducing the likelihood of moisture-related damage over time.
_JPG.jpg)
Water Quality and Backflow Prevention Analysis
-
Comprehensive Water Quality Testing: Tests for contaminants, ensuring water meets health standards, crucial for sensitive facilities like hospitals or schools. This analysis helps prevent health issues by identifying contaminants early, guiding corrective actions.
-
Backflow Prevention Device Inspection: Verifies that backflow preventers function correctly, protecting potable water from contamination. In buildings with multiple water sources, this is essential to ensure cross-contamination doesn’t compromise drinking water quality.
-
Enhancements for Water Quality Compliance: Offers solutions to meet health codes and maintain water safety. For instance, in restaurants or other high-risk facilities, these recommendations help maintain a high standard of water quality and safety for customers and staff.
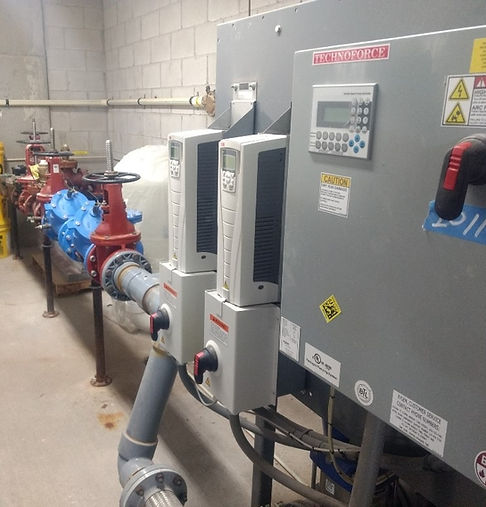.jpg)
Vibration and Acoustic Analysis for Mechanical Systems
-
Vibration Source Identification: Pinpoints equipment or structural elements causing disruptive vibrations, which is particularly beneficial in residential or office buildings where noise impacts occupants. This analysis suggests corrective actions like isolation pads or dampening techniques.
-
Noise Impact Assessment for Occupant Comfort: Measures acoustic levels and suggests solutions to reduce noise, essential for spaces where excessive noise may disrupt work or comfort, like offices, classrooms, or healthcare facilities.
-
Enhancement Recommendations for Stability: Recommends structural or equipment modifications to reduce vibrations and noise. For example, in high-rise buildings with mechanical systems on upper floors, this may involve adding vibration isolators to improve occupant comfort and protect equipment.
.png)
Documentation and Reporting for Legal and Compliance Purposes
-
Clear, Actionable Findings: Breaks down complex investigations into easy-to-understand results, which helps facility managers or building owners understand key issues without technical jargon, supporting informed decision-making.
-
Legally Sound Documentation: Provides reports that meet standards for regulatory, insurance, or legal purposes, crucial for property owners needing documentation for compliance inspections, insurance claims, or legal disputes.
-
Guided Steps for Issue Resolution: Offers a structured action plan, enabling clients to address identified issues confidently and strategically. This is beneficial for clients facing insurance claims or needing to comply with regulatory mandates, as it outlines necessary next steps.
