
CONSTRUCTION ADMINISTRATION SERVICES
Construction Administration services are crucial for the successful execution of your project, ensuring it is completed on time, within budget, and in full compliance with all applicable standards. Our professional oversight during the construction phase helps prevent costly mistakes, ensures quality control, and keeps the project aligned with the original design vision. By managing project milestones, coordinating with contractors, and conducting detailed site observations, we effectively mitigate risks, enhance system performance, and keep the project on track. We take a proactive approach to resolving issues and ensuring adherence to local codes and regulations, safeguarding your investment and securing a successful project. Remember, 'You don't get what you expect, you get what you inspect.' This underscores the importance of diligent inspection throughout the construction process to guarantee the desired results.
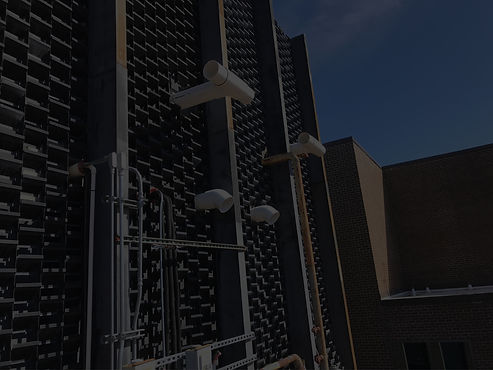
We offer comprehensive Construction Administration services to ensure your mechanical, electrical, plumbing, and fire protection (MEP/FP) systems are installed to the highest standards and fully comply with all relevant codes. Our team ensures design integrity, regulatory compliance, and resolves any issues, minimizing risks and ensuring efficient, on-time project completion.
Expert Oversight for Seamless Project Execution
Our engineering and design services encompass a wide range of critical components that ensure optimal comfort, energy efficiency, and long-term performance. From heating and cooling to advanced ventilation and control systems, we focus on delivering solutions that are not only functional but also sustainable and cost-effective.
Plumbing Systems
Verify plumbing, water piping, and backflow prevention compliance.
RFI Management
Provide timely technical responses and resolve project queries.
Mechanical Systems
Review HVAC, ductwork, piping, insulation, and performance.
Fire Protection Systems
Ensure fire protection systems meet safety and code standards.
Inspections
Ensure construction meets quality standards, specifications, and code compliance.
Electrical Systems
Ensure electrical systems meet design and safety codes.
Site Observations
Conduct site visits to verify installation and compliance.
Additional Services
Troubleshoot system issues and oversee specialized testing.
Submittal and Shop Drawing Review
Verify design compliance and system coordination with specifications
Submittal and Shop Drawing Review
Proper submittal and shop drawing reviews protect the project from delays, cost overruns, and compliance issues, giving clients peace of mind that their project is being executed as planned.
We review submittals and shop drawings to ensure they meet the design intent and project specifications. This process is vital for confirming that all materials and equipment are compliant with the project’s requirements and applicable codes.
-
Scope of Review
-
Space Coordination and Clearances: Prevents conflicts between building systems and ensures that all components fit properly within the designated spaces.
-
Equipment Access and System Performance: Confirms that systems are not only functional but also accessible for maintenance, improving the long-term performance and lifespan of equipment.
-
Applicable Codes and Standards: Guarantees that all designs and materials meet local, state, and federal code requirements, ensuring regulatory compliance and avoiding future liabilities.
-
Conformance to Design Intent and Project Specifications: Ensures that the contractor is adhering to the original design, reducing the risk of costly mistakes or deviations during construction.
-
Compliance with Energy Code Requirements: Verifies that energy-efficient systems are implemented, helping to meet regulatory standards and reduce long-term operational costs for the client.
-
Mechanical Systems
Effective mechanical system reviews ensure that the systems operate efficiently, reduce energy costs, and maintain long-term comfort and reliability in the building.
We ensure that all mechanical system components, from HVAC equipment to piping and insulation, are properly designed, installed, and functioning according to plan. This helps maintain optimal performance, comfort, and energy efficiency throughout the building's lifespan.
-
HVAC Equipment and Systems: Ensures proper heating, ventilation, and air conditioning systems are selected and installed, critical for occupant comfort and energy efficiency.
-
Ductwork Layouts and Fabrication Drawings: Proper ductwork ensures air is distributed efficiently throughout the building, optimizing system performance and comfort.
-
Temperature Control Systems: Guarantees that the building's heating and cooling systems are precisely controlled to maintain a consistent indoor environment, improving comfort and reducing energy waste.
-
Mechanical Room Layouts: Ensures that equipment is laid out to maximize space utilization and ease of access for future maintenance.
-
Piping Systems and Insulation: Ensures that refrigerant, hydronic, steam, and condensate piping are installed for efficient performance and are insulated to prevent energy loss.
-
Vibration Isolation Details: Helps mitigate noise and vibration from mechanical equipment, ensuring a quiet and comfortable indoor environment.
Electrical Systems
Our review process ensures that electrical systems are safe, reliable, and efficient, minimizing the risk of electrical failures and improving building safety.
We provide review and oversight on all electrical components and systems, ensuring proper installation and operation. Our expertise ensures that electrical systems are safe, reliable, and compliant with all applicable codes.
-
Switchgear and Distribution Equipment: Verifies that electrical systems are designed for safe, reliable power distribution, preventing electrical hazards and downtime.
-
Lighting Fixtures and Controls: Ensures that lighting systems are energy-efficient and meet the client’s functional and aesthetic requirements.
-
Power Distribution Layouts: Optimizes the layout of power distribution systems to ensure efficient energy use and minimize system failures.
-
Fire Alarm System Components: Ensures that fire alarms are properly integrated into the building’s safety systems, providing reliable detection and response in case of emergencies.
-
Emergency Power Systems and Low Voltage Systems: Guarantees that critical systems, such as emergency lighting and backup power, are in place to maintain safety during power outages.
-
Lightning Protection Details: Provides necessary protection from electrical surges, ensuring the building’s infrastructure and equipment are safeguarded from lightning strikes.
Plumbing Systems
Well-executed plumbing systems ensure reliability, meet health and safety codes, and contribute to building efficiency, reducing long-term maintenance costs.
Our team oversees the plumbing system, ensuring that all fixtures, piping, and backflow prevention devices are installed in line with design specifications and regulatory standards. This ensures a safe, reliable water supply and effective waste removal for the building.
-
Plumbing Fixtures and Trim: Ensures that all fixtures meet quality standards and functional requirements, improving building efficiency and occupant satisfaction.
-
Domestic Water Piping Layouts: Verifies the water supply system is designed to meet building needs, ensuring adequate pressure and flow to all areas.
-
Sanitary and Vent Piping Systems: Ensures that waste systems are properly vented and draining, preventing potential health risks and system blockages.
-
Hot Water Heating Equipment: Verifies that hot water systems are properly sized and functioning, ensuring that tenants have reliable access to hot water.
-
Backflow Prevention Devices: Protects the potable water supply by preventing contaminants from flowing back into the system.
-
Water Treatment Systems: Ensures that water quality is managed appropriately, especially in areas requiring specialized treatment (e.g., filtration or softening).
Fire Protection Systems
Proper fire protection system oversight is crucial for safety, ensuring compliance with fire safety regulations and protecting both property and lives.
We provide oversight for fire protection systems, ensuring that sprinkler systems, fire pumps, and standpipe systems are installed to code and operate correctly, protecting the building and its occupants.
-
Sprinkler System Layouts: Ensures that fire sprinkler systems are strategically designed to protect the building and its occupants in case of a fire emergency.
-
Fire Pump Assemblies: Verifies that fire pumps are properly installed and capable of supplying water to the sprinkler system, ensuring adequate firefighting capabilities.
-
Standpipe Systems: Ensures that standpipe systems, which are used for firefighting, are installed properly to provide water access to emergency responders.
-
Fire Suppression Details: Ensures that suppression systems, such as foam or chemical agents, are installed where needed, especially in areas with high fire risks.
-
Hydraulic Calculations: Confirms that the water supply and system design meet fire protection requirements to ensure effective suppression.
Site Observations
Site observations help identify and resolve issues early, minimizing delays and ensuring the systems are installed correctly the first time.
We conduct periodic site visits to ensure that MEP/FP systems are being installed according to design and construction documents. This is critical for identifying potential issues early and ensuring the project remains on track.
-
Underground Utility Installation: Ensures that utilities such as water, gas, and electricity are correctly installed, preventing future infrastructure issues.
-
Major Equipment Placement: Verifies that equipment is installed according to specifications to ensure proper functioning and avoid costly rework.
-
Above-Ceiling Rough-In: Ensures that all MEP systems are coordinated in ceiling spaces, avoiding conflicts and delays.
-
System Pressurization Tests and Equipment Startup: Ensures that systems are pressurized and tested for leaks and performance issues before full operation.
RFI Management
Timely and accurate RFI (Requests for Information) responses help maintain project momentum and reduce confusion or miscommunication between contractors and the design team.
We handle technical RFIs related to MEP/FP systems, providing clarifications and supplemental information as needed. This ensures that contractors receive the necessary information to proceed with work, preventing delays.
-
Clear Communication: We facilitate clear communication between all stakeholders, including contractors, engineers, and manufacturers, to resolve issues quickly and efficiently. This reduces confusion and helps maintain project momentum.
-
Coordination with Manufacturers: When necessary, we work directly with equipment manufacturers to provide detailed clarifications or adjustments, ensuring the specified systems are correctly implemented without compromising performance or safety.
-
Documentation & Tracking: Every RFI is tracked through a robust management system, ensuring that responses are documented and all outstanding issues are addressed. This helps maintain accountability and ensures all necessary information is properly documented for future reference.
-
Mitigating Delays & Risks: By addressing RFIs efficiently, we help minimize the risk of costly delays, change orders, or disruptions, thus keeping the project on schedule and within budget.
Special & Progress Inspections
We conduct both special and progress inspections to ensure that all mechanical, electrical, plumbing, and fire protection systems are installed in compliance with the design specifications, building codes, and project requirements.
-
Special Inspections: These inspections focus on critical elements of the construction, such as structural integrity, fire protection systems, and HVAC system installations. We ensure compliance with applicable building codes and standards for systems that require additional oversight, like high-pressure piping or complex fire suppression systems.
-
Progress Inspections: Throughout the construction phase, we perform periodic progress inspections to monitor the installation of systems like HVAC, plumbing, and electrical. These inspections ensure that work is proceeding according to schedule, quality standards are maintained, and any potential issues are identified early.
-
Code Compliance Verification: We ensure that installations adhere to all relevant codes and regulations, verifying that systems are both safe and functional. Any issues are flagged for correction before they impact later phases of the project.
-
Documentation & Reporting: Detailed reports are provided for both special and progress inspections, documenting compliance, issues found, and corrective actions taken. These reports serve as a valuable record for contractors, owners, and project managers.
-
Minimizing Delays & Risks: By providing proactive inspections throughout the project, we help to mitigate risks, avoid costly rework, and ensure that systems meet performance standards.
Additional Services
In addition to our core construction administration offerings, we provide a range of specialized services designed to address complex challenges that may arise during the construction process. Whether it's troubleshooting system performance, overseeing testing, or handling design modifications, our services are tailored to ensure optimal system functionality, code compliance, and seamless project completion. These services are provided as needed, helping you navigate unexpected issues while maintaining the integrity and performance of your MEP/FP systems.
-
System Performance Investigation: We troubleshoot system performance issues, perform energy and acoustic assessments, and verify overall system operation to ensure all systems function efficiently.
-
Design Modifications: We manage any changes to MEP/FP systems during construction, ensuring the modifications are properly integrated and do not affect performance.
-
Specialized Testing Oversight: We ensure that HVAC, electrical, plumbing, and fire protection systems undergo necessary tests to confirm they meet performance standards.
-
Energy Code Compliance: We help with energy modeling and verification to ensure compliance with energy codes, which can result in long-term savings and environmental benefits.
-
Change Order Review: We evaluate any proposed changes to the MEP/FP systems, assess impacts on the overall system, and prepare the necessary documentation for approval.